Leftover fabric, is a pretty standard result of garment and soft-goods manufacturing. The development team explain how the new Samlaren collection challenges that.
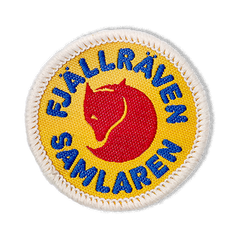
Leftover fabric is a pretty standard result of garment and soft-goods manufacturing. Even for Fjällräven, where the issues of sustainability and reducing waste in production are always top of mind. It is our long-term vision to be the most sustainable outdoor brand after all.
With this in mind, in 2021, designers created a new collection that tackles the challenge of fabric waste head-on: Samlaren. Named after the Swedish word for “the gatherer”, Samlaren is a limited-edition collection made from leftover fabric that was being stored for future use. This fabric was “gathered” to make unique versions of classic Fjällräven designs.
Fjällräven Sustainability Advisor, Christiane Dolva Törnberg explains: “We’ve always had a focus on using resources in a conscious and sustainable way. Actually, the first Greenland Jacket that was produced was developed with a piece of leftover fabric that our founder Åke Nordin had in his garage, that wasn’t suitable for tents. But it turned out perfect for a jacket and that thought of reusing and using resources cautiously has followed us ever since”.
Before exploring the details of the Samlaren collection, we should answer the bigger question: why does leftover fabric happen at all? It usually a matter of standardised order sizes and colour nuance. Sometimes we have to place an order for more fabric than we need. We might need 200 metres of fabric for a season, but the minimum order is 1,000 metres.
We know that we will continue production the following season, so this usually works out well. But sometimes we get large amounts of fabric that is not used the following season if a colour doesn’t sell well. Or something happens with the colour so it is a different nuance from the previous year.
Since organic fabrics are especially susceptible to colour nuance, this is a challenge that Fjällräven is uniquely knowledgeable about. In fact, shifting colours are not a defect, but a natural occurrence that results from factors like water pH levels and humidity at the time of dying.
The Samlaren designers have flipped the script on colour nuance. The entire collection is made of different colours of leftover fabric, which are combined in complimentary and contrasting ways to give each product in the collection a unique look. All while maintaining the same high level of functionality and durability expected of Fjällräven products.
Here is what Global Creative Director Henrik Andersson has to say about the process:
“Samlaren is constructed in the same way and to the same standard as the normal collection. Classic constructions based on typical Fjällräven products that we’ve had for a long time but put together in a quite playful manner”.
We had to go into the design process a little bit from another angle than normally. We needed to look at what we had available and then make the most interesting and functional products out of that.
According to Henrik, putting the collection together challenged their usual approach to design: “We have to go into the design process a little bit from another angle than normally. We need to look at what we have available and then make the most interesting and functional products out of that”.
Christiane explains that the final goal is to become so process efficient that no leftover material is created at all in production:
“Some of the most resource-intense things we can do is to produce fabrics. It requires a lot of water, energy, chemicals. It creates emissions along the way. By creating products from already existing materials, as we do with Samlaren, we can really care for those resources and give them the attention that they deserve.”
That gives us a strange way to look at Samlaren as a future collection. In essence, it is being designed for obsolescence. As Christiane says, “. . . the whole concept lives and dies with our ability to improve and become better and better in our product development”.